Is Electroforming more expensive than Chemical Etching?
Mar 21, 2017 7:00:00 AM By Maarten NijlandAs an engineer, there are a variety of precision metal technologies to choose from, each with their own specifics and (dis)advantages. In our previous blog, we described 6 available precision metal techniques and compared them on runtime and precision. To follow up on this comparison, we compare electroforming with the 5 other precision metal manufacturing techniques, this time on cost-effectiveness.
Electroforming compared with other common precision metal techniques — on cost-effectiveness
Electroforming vs. Chemical Etching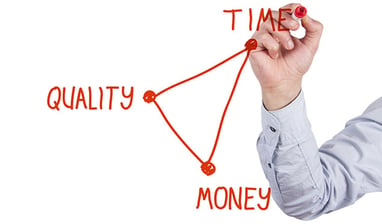
When you require nickel as a material, electroforming will most likely be more cost-effective than chemical etching.
When you do not necessarily require nickel parts, but have multiple options like nickel and stainless steel, costs of electroformed products are not necessarily less than those of etched materials. Other factors like volume, precision, and the desired shape of the contours of your product may influence your decision.
Generally, the rule of thumb is: the higher the precision, the higher the price. So when tolerances are less important, the material is predetermined and the manufacturing costs of this material forms a boundary condition (price aspect), chemical etching wins the race. When micron precision and hole geometry/shape and high repeatability are the main consideration factors, electroforming is definitely your go-to technology. Check out a comparison between the two here!
Electroforming vs. Laser Cutting
When we compare electroforming and laser cutting on cost-effectiveness, it’s also a numbers game. A simple rule of thumb: when you produce a small amount, laser cutting is less expensive; when you produce a large amount, electroforming is less expensive. With laser cutting, you can’t create multiple parts simultaneously. With electroforming, you can. As a result, laser cutting’s lower cost per single item shrinks to insignificance when moving to large scale production.
Electroforming vs. Electro Discharge Machining (EDM) and Micro Milling
We have bundled electro discharge machining (EDM) and micro milling because the same principles apply when we compare them and electroforming on cost-effectiveness: when your volume is small, the cost-effectiveness of electroforming and EDM/micro milling are equal; when you’re going to produce a big volume, electroforming is the most cost-effective option.
Electroforming vs. Micro Stamping
Stamping is a very convenient manufacturing method for engineers. Once you’ve acquired the required tooling, you can create endless replications of your product or component at very low cost. Stamping is particularly cost-effective when you create replications of your product at high volume. That is because the investment in stamping tooling is substantial — so substantial that it becomes unjustifiable when you have a medium volume production running.
If you ‘only’ require 100.000 copies of your product, a stamping tool is just too costly. Electroforming too can produce endless replications of your item at low cost. High replicability is one of the key benefits of electroforming. A rule of thumb: when you aim to produce under a million copies of your item, electroforming is the most cost-effective manufacturing method. Anything above that, and micro stamping is more favorable.
Obviously, cost-effectiveness isn’t the only aspect to factor in when you are comparing manufacturing methods. Precision, freedom of design, and lead and delivery times are also highly important to you as an engineer. Electroforming provides great possibilities in these departments, so the technique might be worthwhile to investigate.
If you would like to learn more about the benefits of electroforming — and how it can drive continuous innovation for you as an engineer — we recommend you check out our electroforming whitepaper. You can pick up your free copy here!