6 precision metal technologies compared on runtime and precision
Feb 8, 2017 7:00:00 AM By Maarten NijlandAs an engineer, there are a variety of precision metal technologies to choose from, each with their own specifics and (dis)advantages. In this blog, we describe 6 available techniques and compare them on runtime and precision.
6 high precision metal technologies explained
Electroforming is an additive manufacturing method to produce metal parts by precise deposition of metals onto patterned substrates. Its uniqueness is that you can grow metal parts atom by atom, providing absolute accuracy and high aspect ratios.
An electrolytic bath is used in this process to deposit metal (nickel, gold, copper) onto a conductive patterned surface; this can be steel or glass. The electroformed part can be harvested from the mandrel, once the material is plated in the desired thickness.
Laser cutting is a precision process that utilizes high energy laser light pulses to provide both accurate apertures and positional tolerances. This process can be enhanced by combining with PCM or PEF technology to provide hybrid solutions such as multi-level stencils. Whatever can be produced by CAD on an X/Y axis is suitable for the laser process.
Chemical etching(also referred to as Photo etching) is a subtractive manufacturing process that removes metal in order to produce a metal part in the desired shape and thickness. The technique stems from optical lithography.
A sheet of the desired material, called a substrate, is first laminated with a layer of light-sensitive resist. The photoresist is then selectively exposed to UV light and developed to obtain a positive image of the product. The metallic product is obtained after exposing the patterned substrate to an etching solution, which selectively removes the unprotected parts from the substrate.
Micro stamping is another manufacturing method to fabricate metal parts from sheets of material. The desired part is cut from metal using hardened steel tools. The part is created in a single strike of the die, as the hardened steel dies are the exact shape of the part. Stamping can also be applied subsequent to other metal processes such as punching.
5. Electro discharge machining (EDM)
The most important part of the process in EDM also takes places in an electrolytic bath, same as Electroforming. EDM disconnects material in small bits by electrical discharging (sparking). The electrolyte in the bath is non-conductive, so a high enough voltage will break down the dielectric and cause a spark. Material is therefore subtracted by a series of rapidly recurring current discharges.
Micro milling is a subtractive metal manufacturing process where you mill material away with a drill. Depending on the milling machine used, drills can automatically change to different sizes and move in different axes, creating complex 2-, 2.5- or 3-dimensional shapes. Accuracy of the structure goes down to a few dozen microns. Almost every material can be milled.
Comparison on runtime and precision
After looking into the 6 typical precision metal technologies, it’s time for a comparison on runtime and precision. In this comparison, we also differentiate runtime between sampling and industrial scale production. This is important because some manufacturing techniques have a very short initial lead time, but a very long runtime for industrial scale production, and vice versa. Runtime of a technology always depends on the complexity of a project, so the values in this table are approximates.
Precision metal technology |
Runtime for a sample |
Runtime for industrial scale production |
Precision |
Electroforming |
Extremely short |
Extremely short |
2-3 μm |
Micro Stamping |
Extremely long |
Short |
50-100 μm |
Chemical etching |
Very short |
Short |
30-40 μm |
Laser cutting |
Extremely short |
Extremely long |
~50 μm |
Electro discharge machining |
Very short |
Short |
~50 μm |
Micro milling |
Extremely short |
Extremely long |
30-40 μm |
Some runtime takeaways
As you can see, some technologies have short runtimes for samples, which makes them ideal for prototyping, and long runtimes for industrial scale production, which makes them unsuitable for, well, industrial scale production. What technique’s best for you really depends on your demand.
So, for instance, if you need a technology that doesn't require high tolerances, but demands an extremely short lead time for prototyping, laser cutting is a good pick. Some technologies, however, have all good qualities combined. Take electroforming for example: because creation of a sample is mainly performed on the actual production line (that’s used for production on an industrial scale), much of the required parameters for your product are already in place when you move from prototyping to mass scale production. This way, there’s no difference in runtime whether your production is on a small or large scale.
If you would like to learn more about the benefits of electroforming — and how it can drive continuous innovation for you as an engineer — we recommend you check out our electroforming whitepaper. You can pick up your free copy here!
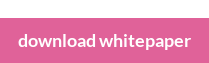