Same game, different name: don’t get fooled by these 8 Chemical Etching synonyms
Aug 23, 2016 10:00:00 AM By Maarten NijlandWhat is the difference between chemical etching and chemical milling? Well, to be honest; there isn’t any. Neither is there a difference between photo etching and chemical etching. In fact, all of the following names describe the exact same process:
- Chemical Etching
- Electrochemical etching
- Photo Etching
- Industrial etching
- Photochemical etching
- Chemical Milling
- Photo milling
- Photochemical milling
- Photo-Chemical Machining (PCM)
How does the chemical etching process work?
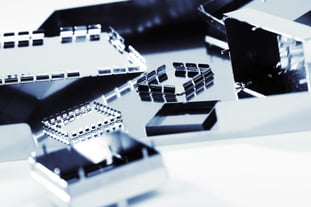
With chemical etching, you subtract (take away) metal in order to produce a metal piece in the desired shape and thickness.
Let’s look into the exact steps for a chemical etching process. As all stages are interdependent of each other, every step in the process is equally important to receive a high quality metal component in the end.
Chemical Etching Materials
A wide range of materials can be photo etched. These include (but are not limited to): a wide range of stainless steels - Mild Steel, Carbon Steel, Tool Steel, Spring Steel - Aluminium - Molybdenum - Nickel Alloys - Copper - Brass, Phosphor Bronze, Beryllium Copper, Nickel Silver - and many others. Rapid prototypes can be produced from drawings in a matter of days.
Chemical Etching Process
First, the metal sheet is cleaned and degreased to ensure a completely clean surface. Then, the sheet of metal is laminated with one or more layers of photoresist. Parts of the photoresist are subsequently exposed to UV light, to obtain an ‘image’ of the desired metal part.
The parts of metal that need to be preserved (resulting in your end product) will be covered. The unshielded parts will be etched in a corrosive chemical solution. This way, the desired metal part will be left behind. Chemical etching is a precisely reproducible process, tolerances quoted on etched features on your parts will typically be +/- 10% of thickness.
Chemical etching is capable of producing highly complex, stress-free, burr-free metal parts with very fine details and tight tolerances. Feel free to ask our specialists for advice on finding the right technique for your innovation and operational breakthroughs.