How electroforming changes the way you design filters and nozzle plates
Feb 15, 2017 7:00:00 AM By Maarten NijlandIn previous blogs, we wrote about what additive manufacturing is. And also how electroforming differs from other types of additive manufacturing. In this blog, we take an even deeper dive into electroforming, and talk about how it changes the way an engineer like yourself works and designs. We focus specifically on the overgrowth part, one of the two electroforming methods (the other one’s electroforming thick resist). To explain the overgrowth process we need to look into the fundamentals of electroforming first.
What is Electroforming
Electroforming is an electrodeposition process. Electrodeposition is the deposition of metal onto a conductive object. Two electrodes (a +ve anode and a -ve cathode) are placed in an electrolytic bath containing a solution of metallic salts and a power source of direct current (DC). While the anode dissolves the material, the cathode builds up the material. In other words, metallic ions are converted into atoms which build up onto the cathode surface through a continuous deposit. Therefore, the material can be built up on micro scale accuracy: atom by atom.
The electroforming overgrowth process (plating)
Now it’s time to look into the overgrowth process. This is how it works [video]. A light sensitive coating is applied on a conductive surface. Artwork, film or glass-tooling is used to expose the light sensitive coating. The coating will polymerise where it is exposed to UV light. After developing the light-sensitive coating the mandrel with conductive and nonconductive areas is ready for electroforming. Metal will grow over the photoresist and size of the aperture is defined by the overgrowth of the electroforming process. Accuracy of the product is therefore defined by the plating process.
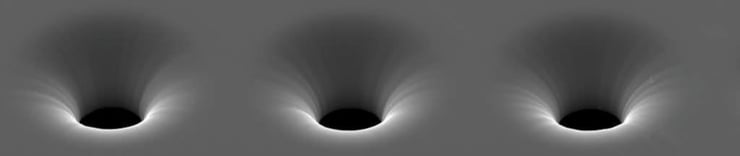
Creating filters and nozzle plates with the electroforming overgrowth process
The overgrowth process is ideal for filters, spray nozzle plates, inkjet nozzle plates, and nebulizer plates. To explain how the overgrowth process will change the way you design, we are going to use creation of filters as an example.
An aperture that’s made with electroforming is small on one end, and grows larger toward the other end. The larger end is where the substance, for example coffee, will exit. What you don’t want in a filter is that undesired parts of a substance pass through it. Take coffee beans for example: you don’t want parts of the actual beans to pass through the filter. The smaller opening end of an electroformed filter won’t allow undesired parts to pass through, because it’s properly sized. The very tight tolerances (down to 2 μm) that electroforming overgrowth process provides allows you to create the exact sizing you desire.
Filters that are created with CNC punching, for instance, won’t possess this exact sizing because the tolerances aren’t as tight with the technique. Walls in punched filters are straight — the filter doesn’t gradually become larger towards the other end. Because the opening at the starting end isn’t small enough, undesired parts of a substance — actual parts of a coffee bean — will pass through the filter, causing it to become constipated over time. This constipation won’t occur with electroformed filters. As you can see, the level of tolerance control we described is crucial when you design your filters, nozzle plates, or other types of high precision components.
With nebulizer plates, the build up is the other way around: the opening end is the larger part, and the component gradually grows smaller toward the other end — the orifice. A tight tolerance is crucial for a highly controlled emission through the orifice. A desirable sizing of the nozzle orifice for proper nebulization is 2 μm. This level of tolerance can’t be achieved with a technique other than electroforming.
As you can see, electroforming allows you to create ultra-precise components for your applications. We definitely recommend you to take an even deeper into electroforming to fully understand the possibilities it provides you as an engineer. To help you do that, we wrote an electroforming whitepaper. You can pick up your free copy here!