Electroforming: the Additive Manufacturing process for micro precision solutions
Feb 25, 2022 6:10:00 PM By Hua FanBased on electrodeposition, electroforming is a unique process that enables the production of accurate metal components with complex features like micro-precision perforations.
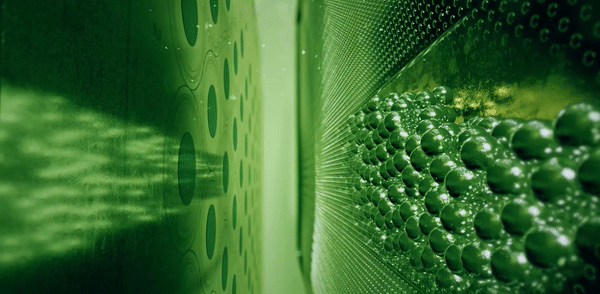
What is electroforming?
Electroforming is a type of metal additive manufacturing method based on the electrodeposition process. In the simplest terms, this means that metal parts are built using a combination of conductive materials, electrolytic solutions, and electric currents. The electroforming technique is particularly well suited to the production of micro-precision metal parts that require tight tolerances and detailed features.
In the electroforming process, a metal blank, known as a mandrel, is placed into a bath of electrolytic solution and two electrodes (an anode and cathode). An electric DC current is passed through the electrodes, which causes metallic ions in the solution to convert into atoms and attach themselves to the mandrel’s surface, gradually building up layers around it. When the desired thickness has been reached, the mandrel is removed from the electrolytic bath and the deposited metal atoms—bonded to each other—are removed from its surface. In the end, the shape of the mandrel determines the shape of the electroformed parts.
Electroforming is overall an extremely effective and precise additive manufacturing technique for metal parts, with notable applications in components that require micro precision.
This approach to electroforming uses a conductive metal substrate, a light sensitive coating, and UV light exposure to produce high precision parts. If we look at Advanced Lithographic Electroforming in more detail, the process consists of six steps:
- Cleaning: in this first step, a conductive metal substrate is cleaned and prepared for the electroforming process.
-
Coating: in this step, the metal substrate is coated with a light sensitive photoresist.
-
Exposure: UV-based Laser Direct Imaging then transfers an image of a part cross-section onto the substrate.
-
Developing: from there, the substrate is developed to process the image, rinsed and then dried.
-
Deposition: the metal substrate is placed into an electrolytic bath and a DC current is applied. The current causes metallic ions to convert into atoms and deposit themselves onto the developed pattern.
-
Harvesting: Once the right thickness of metal has been achieved, the electroformed part can be removed from the metal substrate.
The exponential potential of micro-precision metal parts
One particular area electroforming has proven advantages over other more conventional manufacturing processes, like machining, is in the production of micro-precision perforations. Micro-precision perforations—in other words, metal sheets or parts with extremely fine holes—are utilized in many applications in the food, electronics, and medical industries, among many others.
The electroforming process is ideal for making such micro-perforations and offers several advantages. For one, electroforming is capable of producing perforations with extremely tight tolerances, with feature accuracy down to 1µm. It is also possible to produce very small perforations, with diameters as small as 2 µm, which would be impossible to achieve using machining or punching.
Another benefit offered by electroforming is greater design freedom. Parts requiring micro-precision perforations can integrate various functional features that would be difficult to achieve using subtractive manufacturing, such as high-density perforations and holes with tapered cross-sections. The latter is characterized by an increasing diameter in each hole, which has benefits for filtration applications. Additionally, due to the additive nature of electroforming, micron-scale perforations can be made with perfect edges and no burring.
Electroforming customers also have greater freedom to redesign micro-perforation structures at no additional cost. Because electroforming is a highly scalable process, it can produce one-off parts or multiple production runs cost efficiently. This enables designs to be easily prototyped, tested, and updated, or for multiple different designs to be tested at once. Electroforming also therefore facilitates the transition from prototyping to production.
The wide world of electroforming applications
There are a plethora of applications for electroforming, with several falling into one of the following general categories: filtration, nozzle plates, electronics components, and optical components.
In the category of filtration, electroforming can produce micro-perforation structures for products like espresso machine filters, leaf filters in pressure filtration systems, and filtration screens for food manufacturing. With electroforming, filtration devices can be made with optimized apertures, including tailored perforation size, shape, surface, and edge. By carefully tuning each of these factors, filtration parts can achieve higher performances and reduce the risk of clogging.
Electroforming is also used for the production of nozzle plates, including high-precision inkjet nozzle plates. In fact, many leading inkjet printer manufacturers opt for electroformed nozzle plates to achieve the highest print accuracy. Micro nozzle plates used for various dispensing applications—including fuel injection and medical nebulizers—are also made using electroforming. In this case, the manufacturing process enables the production of micro-scale perforations and a bell-mouth hole structure that enhances jetting performance.
Applications for electroforming in the field of electronics are practically limitless: the technology is used to make parts for hearing aids, shaver foils for electronic grooming devices, nebulizer plates for drug delivery and research, various electronic testing tools like contactors, and more. In the production of components for electronic devices, precision is of the utmost importance, and electroforming offers the tolerances and high-quality needed.
Electroforming can enable innovation in a wide range of applications from consumer good to medical deives. Image credit: Veco.
The same is true for the manufacturing of high-precision optical components. Manufacturers of aperture plates—used in cameras, endoscopes, gamma-ray detectors, and more—turn to electroforming for its unparalleled precision, design freedom, and, crucially, its capacity to produce smooth, burr-free parts. The process is also common for making encoder discs used in factory automation, robotics, and other cutting-edge applications.
Conclusion
Electroforming's ability to create highly precise, detailed metal parts at competitive costs makes it an important choice within additive manufacturing. Its applications in emerging areas such as PIC and aerospace will also continue to expand. Further, collaborative and flexible approaches to working with designers from manufacturing suppliers such as VECO are enabling hardware designers at all scales to take engage with the advantages for electroforming.