Electroforming for Engineers: getting started with Electroforming step by step
Nov 29, 2023 8:41:07 AM By Hua FanFor engineers with a demand for complex metal components that require high precision and accuracy, Electroforming may be the ideal fabrication method to realize the design specifications. This article helps engineers assess if Electroforming is a suitable solution and how to proceed with successfully transferring engineering design into high-quality components step by step.
1. learn the basics of Electroforming
Electroforming is a versatile metal-forming process that allows engineers to create complex, high-precision metal parts with ease. Combining high-accuracy lithography with Electrodeposition builds up products in the desired shape and thickness with ultimate control. Intricate geometries, fine details, and smooth surfaces unachievable through other fabrication methods can be easily achieved with Electroforming cost-effectively and with excellent repeatability.
In comparison with other manufacturing technologies
Electroforming stands out with its high accuracy, short lead times, low costs, burr-free parts, design flexibility, surface replication abilities, and unchanged material properties. It is the technology of choice for high-volume production of complex, ultra-precision metal components across industries.
-> Electroforming vs Laser Cutting
-> Electroforming vs 3D printing
2. confirm design feasibility with the Electroforming technology
technical features:
geometry: freedom of design for intricate metal components
precision: feature size down to 2 microns, with tight tolerances below 1 micron.
accuracy: position accuracy achievable with Electroforming reaches micron level.
dimensions: product size up to 1370*1370mm, thickness from 5µm to 1200 µm
cross sections: straight-walls, tapered profiles, and bell-mouth shapes can be provided.
5D: Multi-layer solutions allow designing beyond a 2D plane.
production volume: mass volume (fast prototyping supported).
common applications by market:
filtration: Sieves used in aerospace, defense, pharmaceutical, food processing, oil refinery, water treatment, research, and other industries
digital printing: inkjet nozzle plates, filter plates, or nozzle guards
electronics/semiconductor: testing contactors, cantilevers, test probes, lead frames, and electrical parts in medical devices such as hearing aids
medical: precision metal sieves and meshes e.g. for nebulizers, flow regulation parts
optical components: spectrometer slits and apertures, beam selectors, and encoder discs
-> learn more about capabilities and applications of Electroforming
3. explore material options of the Electroforming technology
Veco offers engineers a wide selection of material options to suit their specific application needs. Nickel and copper remain the most commonly used materials in the Electroforming process. However, besides copper, Veco also provides a range of proprietary nickel options with enhanced properties. These include:Meta-Nickel: Offers improved thermal resilience and mechanical strength compared to standard nickel. Ideal for high-performance applications.
Sulfamate Nickel: A non-reflective nickel that provides high ductility and can endure heat treatment such as laser cutting or welding. Useful for freedom in further assembly and specific optical properties.
Palladium-Nickel: Combines bio-compatibility with superior corrosion resistance. Suitable for medical devices and implants.
HR-Nickel: Exhibits excellent thermal stability at high temperatures. Applicable in aerospace and automotive industries.
Veco84: A high-hardness nickel alloy developed by Veco. Delivers increased hardness and tensile strength.
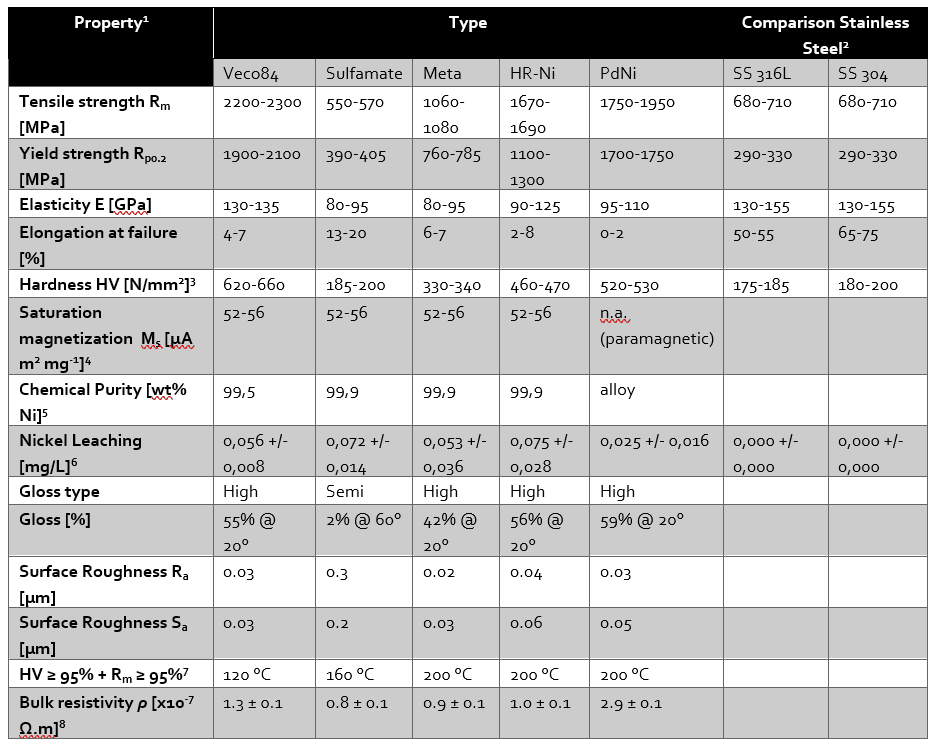
functional coatings to augment the characteristics of Electroformed components:
- Anti-reflective coatings improve optical clarity by reducing glare. Essential for high-precision optical systems.
- Highly reflective coatings maximize light reflection. Used in solar panels, reflectors, and lighting fixtures.
- Wear-resistant coatings extend the component lifetime in high-friction environments.
- Corrosion-resistant coatings protect against degradation from chemicals, fluids, or salt spray.
-> check materials and properties in detail
4. co-engineering with our application engineer team
To achieve the best possible solutions for the critical precision components in demand, Veco provides co-engineering support from initial design through prototyping and scaling to efficient industrial production:
- identify micro-precision challenges
- envision solutions with the engineering team
- rapid prototyping and iteration
- seamless transition to volume production
-> learn more about co-engineering with our team
5. quality assurance
Parts manufactured at Veco can be produced in a variety of cleanroom environments. To consistently provide and guarantee our customers with the best quality, Veco has been certified to the latest version of the ISO9001 quality management system. In addition, we use the Six Sigma method for continuous improvement of the quality of the processes.
-> learn more about our quality standards here
Veco’s two-step quality inspection:
- After every sample production, we produce a first article inspection report (FAIR)to ensure all the key parameters are within the predefined bandwidth.
- After the quantitative inspection, a qualitative inspection to ensure the sample is created according to the quality requirements.