What electroforming can bring for medical device design engineers?
Feb 28, 2017 7:00:00 AM By Harrie KnolIn the medical industry, engineers are often challenged with designing and development for the next innovation. Electroforming, highly suitable to create thin, strong, and/or ultra-precise components in complex shapes, has already proved to be a great solution in many medical applications. It has also provided outcome in many situations where cost-effective production was needed.
This blog reviews what Electroforming can do for the next breakthrough in Medical Device Industry and presents examples of how it has been driving innovation in the industry.
Millions of droplets per second: our nebulizer plate solutions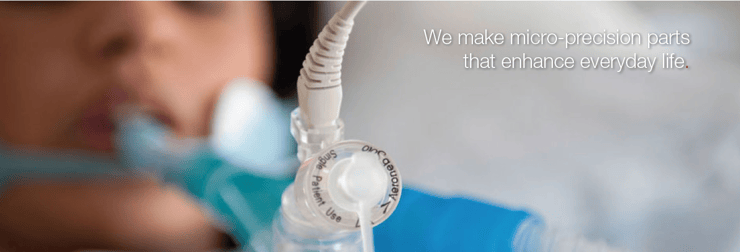
In state of the art drug delivery systems enabled by Vibrating Mesh Technology, Veco’s nebulizer nozzle plate releases millions of micron sized droplets per second through its unique geometry, forming a perfect fine mist for targeted delivery to the lung.
The industry sees an increasing demand for nebulizer plates of very high precision. Electroformed nozzle plates do meet this demand with uniform orifice holes down to 2 micron.
Veco has been working together with leading companies in drug delivery system research and development. With our in house micro electroforming technology, nebulizer plates are fabricated with bio-compatible materials with micro orifice hole size.
Miniaturized hearing aid electronics: Our hearing aid solutions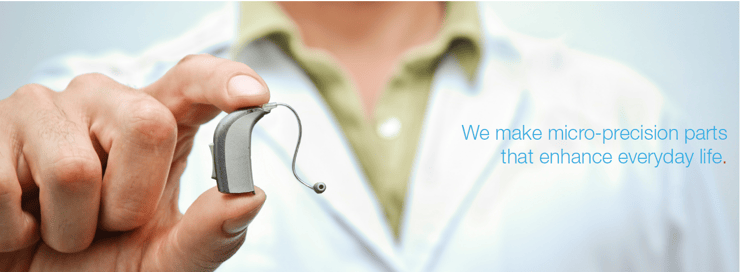
Veco has been providing hearing aid manufacturers with innovative and efficient micro-sized components such as shock plates and miniature spacers used in hearing aid instruments.
As a world leading specialist in precision engineering with integrated in house capabilities of electroforming, photo etching and laser cutting, we are able to produce, atom by atom, stress- and burr-free precision metal parts with tight tolerances.
Every Molecule Counts: our accurate flow control solutions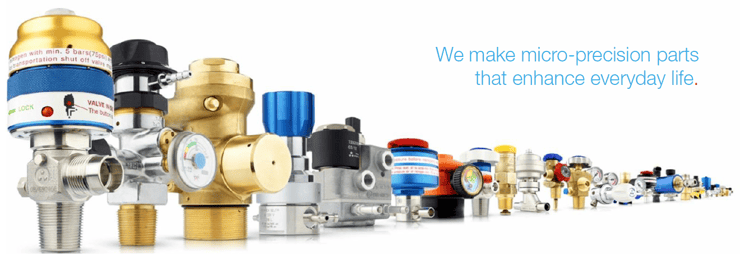
A flow disc is a thin metal part with micro apertures to accurately control flow stream. It is widely used in flow meters/regulators that require high accuracy of dispensing control, e.g. flow regulators for medical dispensing, flow meters for industrial gas control, etc. Quality and accuracy of the orifice disc is of key importance in any flow regulating/measurement system since it determines the dispensing control of the whole system: A 5% variation of a hole diameter could result in a 10% variation of the flow quantity.
Electroforming is known as the perfect fabrication method for high accuracy flow discs with customer designed patterns . Hole geometry is in perfect control which enables accurate and consistent dosing performance.
If you want to know more about what Electroforming can bring to Medical industry, or to find out possibilities with other industries, check out our Whitepaper on Electroforming.